Conductive slurry mixing requires high uniformity and dispersion.CoNele intensive mixer with its unique design,performs well in the preparation of electronic materials.The following are key analyses and suggestions:Lithium battery mixer-lithium battery slurry disperser-lithium battery high-speed mixer manufacturer1.Mixing requirements of conductive slurryMaterial characteristics:high solid content(such as silver powder,carbon nanotubes),high viscosity,and agglomeration must be avoided.Process requirements:Uniform dispersion:conductive particles must be free of agglomeration and evenly distributed.Low pollution:avoid metal pollution,and the material must be stainless steel or ceramic coating.Temperature control:prevent overheating from causing solvent volatilization or material denaturation.No bubbles:affect the subsequent coating process.Conductive slurry mixer
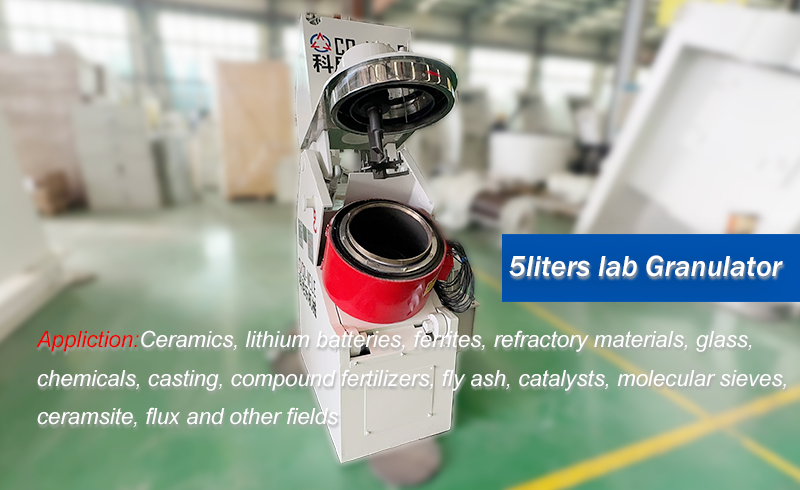
2.Advantages of CoNele intensive mixerTilted design:Dynamic mixing:The cylinder is tilted(usually 15-30°),combined with rotating blades to form a three-dimensional vortex and reduce dead angles.Efficient discharging:The tilted design facilitates the pouring of slurry,which is suitable for high-viscosity materials.Strong shear and convection:The high-speed rotor(speed can reach 100-2000rpm)generates high shear force,which effectively breaks up agglomerated particles.The spiral blade pushes the material up and down to improve the uniformity of dispersion.Temperature control capability:The jacket cooling/heating system can be optionally equipped to control the mixing temperature within the range of 25-60℃,which is suitable for sensitive materials.Material and seal:The contact parts are made of 316L stainless steel or wear-resistant coating to avoid pollution.The sealing design is dust-proof and anti-volatile,suitable for organic solvent systems.Parameter adjustability:The speed,tilt angle,and mixing time can be programmably controlled to adapt to different formulas(such as silver paste,graphene slurry).3.Potential problems and solutionsHigh shear leads to material structure damage:Recommendation:Use a segmented mixing strategy,premix at low speed first,and then gradually increase the speed.Difficulty of equipment cleaning:Recommendation:Choose a quick-opening structure design with a CIP(online cleaning)system.High initial investment cost:Recommendation:Compare the long-term production efficiency improvement(such as 30%-50%reduction in mixing time)with the energy consumption reduction to evaluate ROI.4.Slurry mixer selection recommendationSmall batch R&D:Select a 1-50L small experimental model(CEL01 intensive mixer).Mass production demand:Select a 100-7000L specification intensive mixer to match the production line capacity.Speedrange:0-1500rpm(stepless speed regulation).Temperature control accuracy:±2℃.Sealing level:IP65 or above(anti-solvent evaporation).Conele Machinery Company provides a free test center to provide customers with a one-stop free trial service.5.Industry application casesLithium battery companies:used for graphene conductive slurry production,the slurry resistivity is reduced by 15%after dispersion,and the batch stability reaches 98%.Photovoltaic silver paste preparation:mixing time is shortened to 40%of traditional equipment,and the silver powder dispersion uniformity(CV value)is<3%.CoNele intensive mixer is suitable for mass production of medium and high viscosity conductive pastes,especially in terms of dispersion efficiency and process controllability.It is recommended to prioritize the evaluation of actual material properties and conduct machine trials to optimize process parameters.
Tags:
intensive mixer
Lithium battery slurry mixer
Back To The List