Efficient mixing and uniform dispersion - revealing the core equipment for tungsten carbide powder manufacturing[Industry background]
Tungsten carbide (WC) powder is the main raw material for cemented carbide, cutting tools and wear-resistant parts, and its quality directly affects the performance of the final product. In the production process of tungsten carbide powder, high-intensity mixers have become an indispensable key equipment. According to statistics, nearly 90% of tungsten carbide powder manufacturers in the world use high-intensity mixers for raw material pretreatment instead of traditional mixing equipment. What is the reason behind this?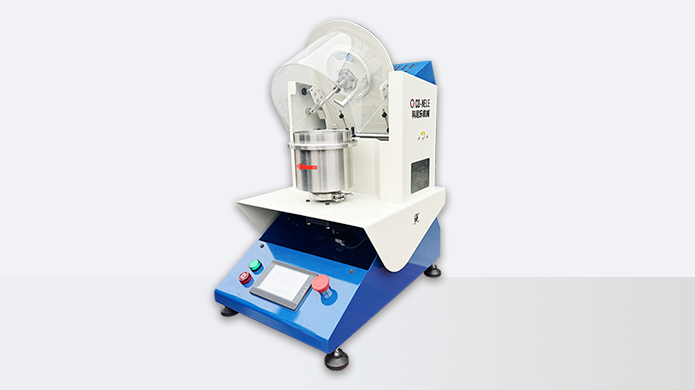
Mixing challenges of tungsten carbide powder
The production of tungsten carbide powder requires uniform mixing of tungsten powder, carbon black and other additives to ensure the consistency of subsequent carburization reactions. However, traditional mixing equipment (such as V-type mixers and double cone mixers) has the following problems:Uneven mixing: Powder is easy to stratify, resulting in composition fluctuations;Inefficiency: Long mixing time and high energy consumption;Pollution risk: Mechanical friction may introduce impurities.Inclined design + three-dimensional intensive mixingCompared with traditional equipment, the intensive mixer perfectly adapts to the production needs of tungsten carbide powder through high shear force + convection mixing mechanism:
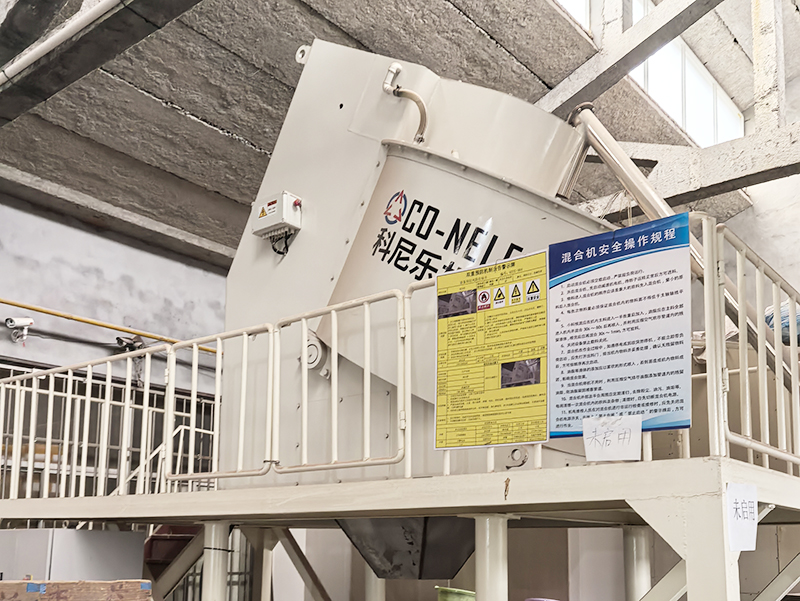
✅ Ultra-high uniformityThe high-speed rotor + stator structure makes the powder tumble violently in three-dimensional space to ensure nano-level dispersion of WC and carbon black.Actual measured data: The composition deviation after mixing is <0.5%, which is much better than the 3%~5% of traditional equipment.✅ High efficiency and energy savingThe mixing time is shortened by 50%~70% (usually only 10~15 minutes), greatly improving production capacity.Case of a well-known cemented carbide company: After replacing the intensive mixer, the annual production capacity of a single line increased by 30%.✅ Adapt to complex formulasIt can handle mixed systems containing binders such as paraffin and PE, directly meeting the subsequent pressing and molding needs.✅ Low pollution designFully enclosed structure + wear-resistant lining (such as tungsten carbide coating) to avoid the introduction of metal impurities. Industry application examples in tungsten carbide powder high-intensity mixers
Case 1: Germany's top cemented carbide manufacturerProblem: The density of tungsten carbide powder produced by traditional mixers fluctuates greatly after sintering (±0.3g/cm³).Solution: Using the CR500 inclined intensive mixer, the density consistency of sintered products is improved to 99.2%;Case 2: A Chinese silicon carbide ceramic companyDemand: Highly uniform mixing of silicon carbide (SiC) and sintering aids (Al₂O₃-Y₂O₃).Effect: After CO-NELE CR series intensive mixing, the bending strength of ceramic sintered bodies is increased by 15% Future trends: intelligence and greater production capacity
As the cemented carbide industry develops towards ultrafine and nano-scale powders, the new generation of intensive mixers are integrating:Online monitoring system (real-time control of speed and temperature);AI optimizes mixing parameters (such as automatic matching programs for different WC particle sizes);Modular design (single processing volume can reach more than 5000L).
Tags:
Tungsten carbide powder high-intensity mixers
Intensive mixer
high-intensity mixers
Back To The List