CO-NELE's unique sand mixing process ensures stable/reproducible sand quality, unaffected by other factors in the process, and provides a perfect 3D printing sand mixing system solution.
Sand and extensive expertise in pre-mixing, homogenization, moisture content testing and correction, final mixing and unloading. When the unloading door is opened, the composite sand is ready for use - with optimal flow characteristics, uniformity and non-agglomerated consistency
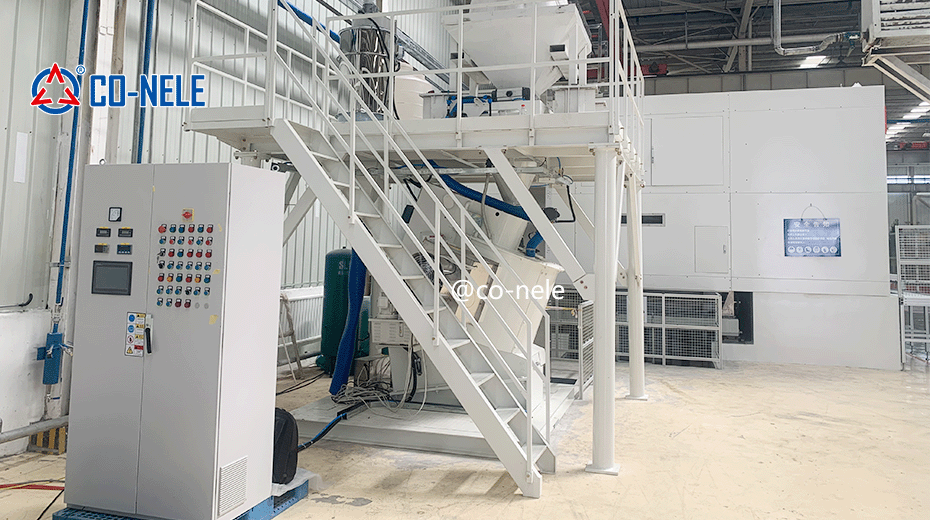
Core features of 3D printing intensive foundry sand mixer
Efficient sand mixing system:
Fast and uniform: The inclined design makes the movement of sand and curing agent more complex during the mixing process, improves the strength and consistency of the sand mold, and ensures that uniform mixing is achieved quickly.
Fast sand mixing speed, high production efficiency, and greatly shortened production cycle.
Flexible and adjustable:
Adjustable speed: The speed can be adjusted according to the characteristics of the sand to optimize the mixing effect.
Adjustable inclination angle: By adjusting the inclination angle of the cylinder, the mixing time and intensity can be controlled to adapt to different process requirements.
Reasonable structural design:
Compact design: Small footprint, suitable for environments with limited space.
Strong durability: Wear-resistant materials are used to extend the life of the equipment and reduce maintenance costs.
Easy operation:
Integrated PLC control system realizes full process automation from sand mixing to printing, reducing manual intervention.
Supports one-button start, automatic cleaning, fault diagnosis and other functions, simple and convenient operation
Energy saving and environmental protection:
Low energy consumption: Efficient sand mixing reduces energy consumption and reduces operating costs.
Adopts closed design: The sealed structure reduces dust and noise and improves the working environment.
Flexibility and compatibility:
Can handle a variety of sand particles (such as quartz sand, ceramic sand) and binders (such as furan resin, water glass), adapting to different casting materials.
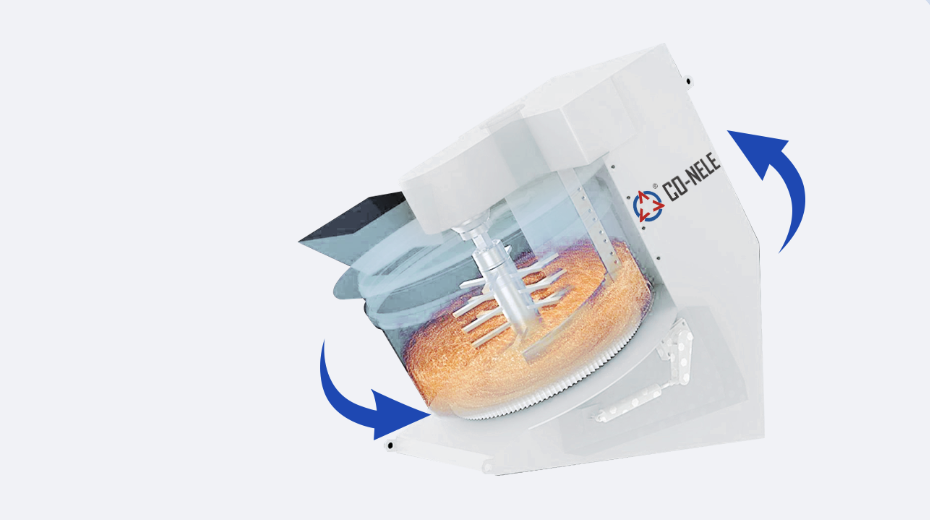
3D printing intensive foundry sand mixer principle and its core structure
Material mixing principle: Through the rotation of the agitator, the sand, binder, curing agent and other materials are fully mixed in the mixing barrel. Parameters such as the shape, size and speed of the agitator will affect the mixing effect, ensuring that various materials can be evenly distributed in the mixture to meet the requirements of 3D printing for sand performance.
Heating and temperature control principle: The sand mixer is usually equipped with a hot air heating device and a stirring temperature sensor. The stirring temperature sensor monitors the temperature of the material in the stirring barrel in real time and feeds back the temperature signal to the hot air heating device. The hot air heating device automatically adjusts the temperature and flow of the hot air blown into the stirring barrel according to the feedback signal, so that the sand material reaches and maintains a constant temperature.
The working principle of the inclined high-power foundry sand mixer is mainly based on the following ⑤ aspects:
① Inclined cylinder and gravity: The cylinder of the casting sand mixer is installed at a certain tilt angle. When the cylinder rotates, the molding sand continuously rises and falls along the inner wall of the inclined cylinder under the combined force of gravity and centrifugal force, forming a complex flow pattern, so that the molding sand can be initially mixed and turned in both horizontal and vertical directions, and a large range of molding sand exchange can be achieved.
② Shearing and stirring of high-speed rotor: The casting sand mixer is equipped with a high-speed rotor inside, and the rotor is usually installed in an eccentric position. When the rotor rotates at high speed, it will produce strong shearing, impacting and stirring effects on the surrounding molding sand, refine and disperse the molding sand, make the contact between the molding sand more sufficient, achieve high-precision mixing, and allow the molding sand of different components to be evenly distributed in the mixture.
③ Assistance of multifunctional scraper: The multifunctional scraper in a fixed position plays an important role in the mixing process. On the one hand, it can disrupt the flow direction of the material, prevent the molding sand from forming a fixed flow path, and ensure that the molding sand can fully participate in the mixing; on the other hand, the scraper can transport the molding sand to the mixing range of the high-speed rotor, so that the molding sand can better accept the shearing and stirring of the rotor, and at the same time prevent the molding sand from sticking to the wall and bottom of the mixing disk, ensuring the continuity and uniformity of the mixing.
④ Coordinated movement of rotating parts: The sand mixing disk and the high-speed rotor generally rotate in opposite directions, but can also be set to rotate in the same direction according to the special process requirements of the molding sand. This rotation method makes the molding sand form a complex motion trajectory in the mixer, generating stronger relative motion and friction, further enhancing the mixing effect.
⑤ Parameter adjustment and control: Multiple parameters of the inclined intensive mixer can be adjusted according to different material characteristics and process requirements, such as rotor speed, mixing disk speed, cylinder inclination angle, mixing time, etc. By accurately adjusting these parameters, precise control of the mixing process can be achieved to meet the requirements for material mixing in different production scenarios and obtain the required mixing effect and product quality.
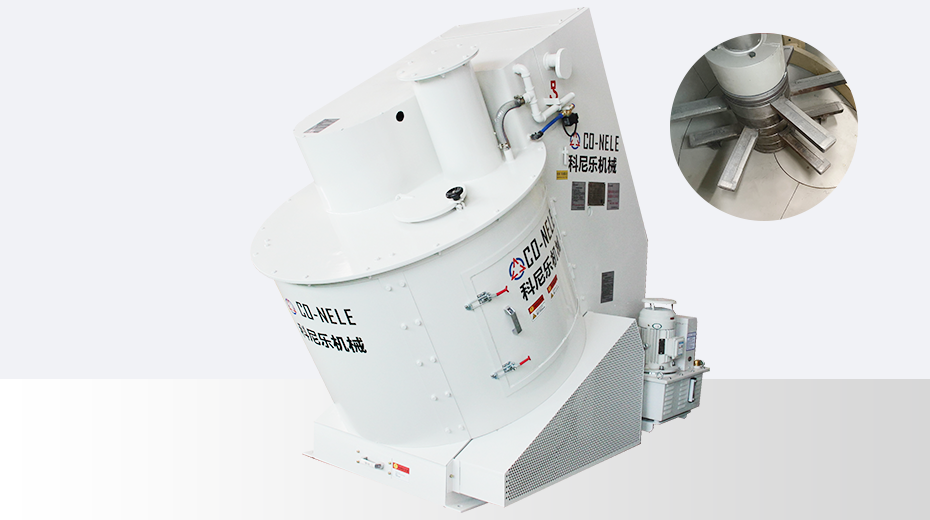
Why choose CO-NELE intensive mixer for 3D printing foundry sand mixer?
Ensure sand quality: It can evenly mix sand, binder and other materials to make the performance of sand stable and consistent, thereby improving the quality of 3D printing sand molds and ensuring that the strength, precision and surface quality of sand molds meet casting requirements.
Improve production efficiency: Accurate material metering and efficient mixing functions can shorten the sand mixing time and quickly provide qualified sand for 3D printing equipment, which helps to improve the efficiency of the entire casting 3D printing production process and achieve continuous and efficient production.
Reduce costs: By accurately controlling the amount of materials, the waste of sand and binder is avoided, and the cost of raw materials is reduced. At the same time, the sand mixer has a high degree of automation, which reduces manual intervention and labor costs.
Improve product quality stability: Stable sand temperature and uniform mixing quality make the quality of the sand mold printed each time more stable, reduce sand mold defects and scrap rate caused by sand problems, and improve product consistency and reliability.
3D printing foundry sand mixer workflow
Model design: Use CAD software to design the 3D model of the sand mold.
Slicing: Slice the 3D model to generate printing paths and parameters.
Sand mixing: Mix the sand and binder in proportion to ensure uniform mixing.
Printing: The sand mold is printed layer by layer through the 3D printing system, and the binder bonds the sand into shape.
Curing: After printing, the sand mold is cured by a curing device to enhance strength.
Cleaning: Clean the excess sand and binder on the surface of the sand mold and prepare it for casting.
CO
-NELE Intensive foundry sand mixer application areas
• Automobile manufacturing: complex castings such as engine blocks, cylinder heads, turbochargers, etc.
• Aerospace: high-precision turbine blades, engine parts.
•Industrial equipment: pump and valve housings, gearboxes, and large mechanical parts.
•Artwork casting: complex sculptures, personalized artworks.
•R&D trial production: rapid prototype verification, shortening product development cycle.