Select CO-NELE vertical axis planetary mixer (model: CMP750) with hanging roller forming process to replace the traditional twin-horizontal shaft mixer. Improve the quality and production efficiency of Φ300-1500mm reinforced concrete drainage pipes.Key configuration and process of concrete drainage pipe productionSelection of vertical axis planetary mixerModel: CMP750 (capacity 750L, power 30kW)Advantages:Planetary motion (revolution + rotation) realizes dead angle mixing and solves the problem of uneven distribution of fiber and aggregate (pipe piles need to be mixed with polypropylene fiber).The mixing time is shortened to 60 seconds/plate, and the homogeneity reaches more than 95% (the measured concrete segregation rate is <0.8%).The lining and blades are made of high chromium alloy wear-resistant material, and the service life is increased by 2 times compared with traditional equipment.
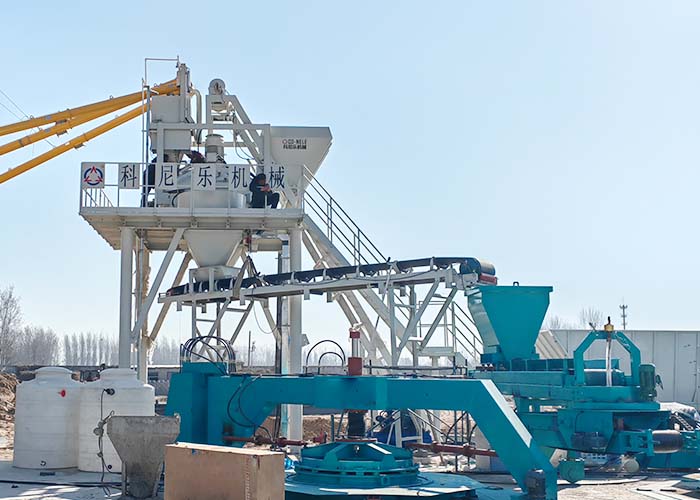
Concrete mix designC40 pipe pile concrete:Cement (P.O 42.5): 380kg/m³Aggregate (5-15mm granite): 1200kg/m³Fiber content: 0.9kg/m³Water-cement ratio: 0.32 (add water-reducing agent to adjust the slump to 30-50mm)Mixing effect: The vertical shaft mixer has significant adaptability to low slump concrete, and the fiber dispersion is not agglomerated by naked eye.Concrete drainage pipe suspension roller production processSteps:Mix station centralized feeding → 2. Feeding machine feeds suspension roller forming machine → 3. Roller forming (roller pressure 15-20MPa) → 4. Steam curing (80% strength in 12 hours) → 5. Demolding and stackingMatching improvement:Pneumatic gates are installed at the mixer outlet to control the unloading speed and avoid uneven accumulation of material layers in the suspension roller mold.The mixing cycle is synchronized with the workstation rhythm of the suspension roller machine (one pipe every 5 minutes), and the production capacity is increased by 30%.
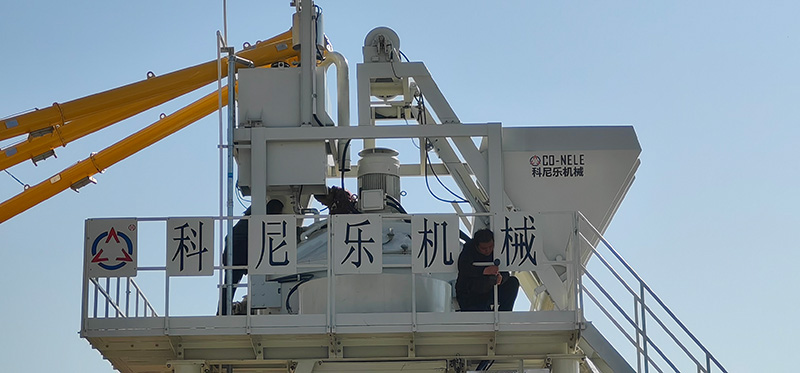
On-site measurement resultsQuality indicators:The standard deviation of the compressive strength of the pipe body is reduced from the original 3.5MPa to 1.8MPa (strength stability is improved).The smoothness of the inner wall is improved (no aggregate peeling phenomenon during the suspension roller forming stage).Economic benefits:Power consumption is reduced by 18% (the power utilization rate of the vertical shaft machine is higher).The equipment failure rate is reduced from an average of 5 times per month to 1 time (reducing mold wear caused by uneven mixing).Industry application suggestionsSelection and matching: The vertical shaft planetary mixer is more suitable for the production of high-grade, fiber/steel fiber reinforced pipe pile concrete. Ordinary pipe piles can use low-power models to reduce costs.Maintenance points: Regularly check the lubricating oil status of the planetary gearbox (maintenance is once every 100 hours for the first operation, and it is recommended to replace it every 500 hours in the later period).Environmentally friendly adaptation: It can be connected to the dust recovery system of the mixing station to meet the requirements of green production (actual dust emission <20mg/m³).The combination of the vertical axis planetary mixer and the suspension roller process significantly improves the quality consistency and production efficiency of concrete pipes, especially for high-demand pipe pile projects. In actual applications, parameters need to be optimized according to the differences in pipe diameter and formula.